

Polished concrete is the ultimate no-wax flooring material. With the proper floor grinding equipment and experience, concrete polishing contractors can grind concrete surfaces, whether new or old, to a high-gloss finish. Factor in the superior durability and performance of concrete, and it’s no wonder why retail, commercial warehouse and office facilities, and even homeowners are catching on to the appeal of these smooth, high-lustre floors.
WHAT IS POLISHED CONCRETE?
Heavy-duty machines are used to gradually grind down a concrete surface to the desired degree of shine and smoothness, similar to sanding wood.
WHERE CAN POLISHED CONCRETE BE USED?
The most common places polished concrete is used include:
- Large warehouses and warehouse outlets
- Retail stores
- Hotels and restaurants
- Office buildings
- Auto showrooms
- Private residences
BENEFITS OF POLISHED CONCRETE FLOORING
Homeowners, retailers, big-box stores, educational and medical facilities are choosing polished concrete for their floor finish because of the competitive advantage polished flooring offers over other types of floor coverings. Decorative concrete in the form of polished floors has become the logical choice because of the great value it delivers, and because it can compete aesthetically as well.
Residential Benefits:
- Cost savings: Traditional floor covering materials are not necessary when the slab on grade is used as the finished floor surface
- Longer life-cycle savings: Polished floors are not as vulnerable to damage as other materials and do not need replacing
- Easy to clean: Won’t harbor dust, dirt, allergens
- Available in wide variety of colours and designs
Commercial and Retail Benefits:
- savings: Using the slab on grade as the finished floor surface is more cost effective, maintenance costs are lower.
- More resistant to high foot traffic. A grocer in Tennessee explains that he is able to maintain primarily just the traffic ways within his store, which saves time and money because he does not have to move large display cases to wax and strip the floor.
- Less maintenance and longer service life: Polished floors are easy to clean, requiring only occasional damp mopping. They also eliminate the need for messy waxes or coatings as well as the associated labour, time, and expense to apply them. The glossy surface of polished concrete resists the marks of forklift truck tires and staining from oil and chemical spills.
- Resistant to moisture transmission issues: Polished concrete allows the floor to breathe and eliminates issues that arise with other flooring materials that seal off the concrete, such as tile, etc.
- High light reflectivity: Important for office building floors, hotels, restaurants, and other public facilities that want to project a bright, clean, professional image. Also saves energy by reducing artificial lighting requirements.
- Is a sustainable flooring alternative: Polished concrete does not require hazardous coatings, cleaners or adhesives.
CAN ALL CONCRETE BE POLISHED?
Almost any structurally sound concrete floor, whether old or new, can be polished with proper preparation. However, there are some exceptions. See how to determine your floor’s suitability for polishing.
STEPS OF THE CONCRETE POLISHING PROCESS
An overview of how concrete floors are polished
A polished concrete floor has a glossy, mirror-like finish. The design options for polished concrete are vast. You can choose nearly any colour, create patterns with saw cuts, or embed aggregates or interesting objects into the concrete prior to polishing. The reflectivity of the floor can also be controlled by using different levels of concrete polishing. Polished concrete is popular in commercial buildings because it is easy to maintain. Maintaining polished floors requires dust mopping and occasional use of a cleaning product.
Simply put, polishing concrete is similar to sanding wood. Heavy-duty polishing machines equipped with progressively finer grits of diamond-impregnated segments or disks (akin to sandpaper) are used to gradually grind down surfaces to the desired degree of shine and smoothness.
Concrete Polishing Process
The process begins with the use of coarse diamond segments bonded in a metallic matrix. These segments are coarse enough to remove minor pits, blemishes, stains, or light coatings from the floor in preparation for final smoothing. Depending on the condition of the concrete, this initial rough grinding is generally a three- to four-step process.
The next steps involve fine grinding of the concrete surface using diamond abrasives embedded in a plastic or resin matrix. Crews use ever-finer grits of polishing disks (a process called lapping) until the floor has the desired sheen. For an extremely high-gloss finish, a final grit of 1500 or finer may be used. Experienced polishing crews know when to switch to the next-finer grit by observing the floor surface and the amount of material being removed.
During the polishing process an internal impregnating sealer is applied. The sealer sinks into the concrete and is invisible to the naked eye. It not only protects the concrete from the inside out, it also hardens and densifies the concrete. This eliminates the need for a topical coating, which reduces maintenance significantly (versus if you had a coating on it). Some contractors spread a commercial polishing compound onto the surface during the final polishing step, to give the floor a bit more sheen. These compounds also help clean any residue remaining on the surface from the polishing process and leave a dirt-resistant finish.You can polish concrete using wet or dry methods. Although each has its advantages, dry polishing is the method most commonly used in the industry today because it’s faster, more convenient, and environmentally friendly. Wet polishing uses water to cool the diamond abrasives and eliminate grinding dust. Because the water reduces friction and acts as a lubricant, it increases the life of the polishing abrasives. The chief disadvantage of this method is the clean-up. Wet polishing creates a tremendous amount of slurry that crews must collect and dispose of in an environmentally sound manner. With dry polishing, no water is required. Instead, the floor polisher is hooked up to a dust-containment system that vacuums up virtually all of the mess.
Many contractors use a combination of both the wet and dry polishing methods. Typically, dry polishing is used for the initial grinding steps, when more concrete is being removed. As the surface becomes smoother, and crews switch from the metal-bonded to the finer resin-bonded diamond abrasives, they generally change to wet polishing.
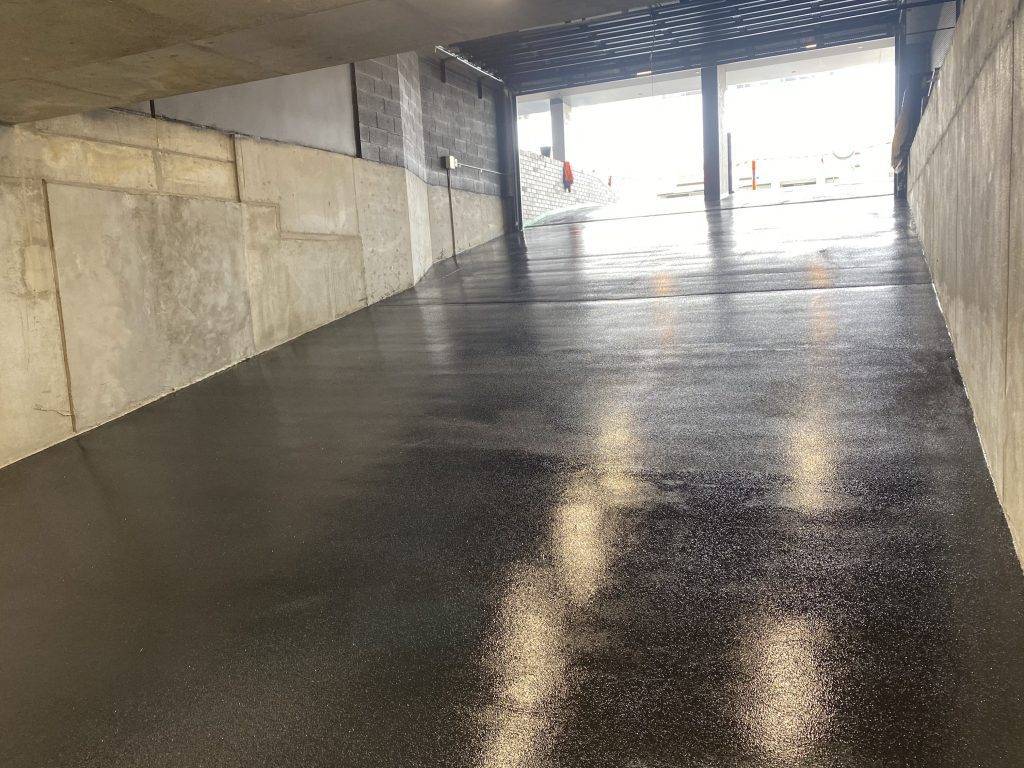
Driveway Restoration
Concrete driveway restoration due to erosion is common. Erosion can create a sunken or cracked drive....
Read More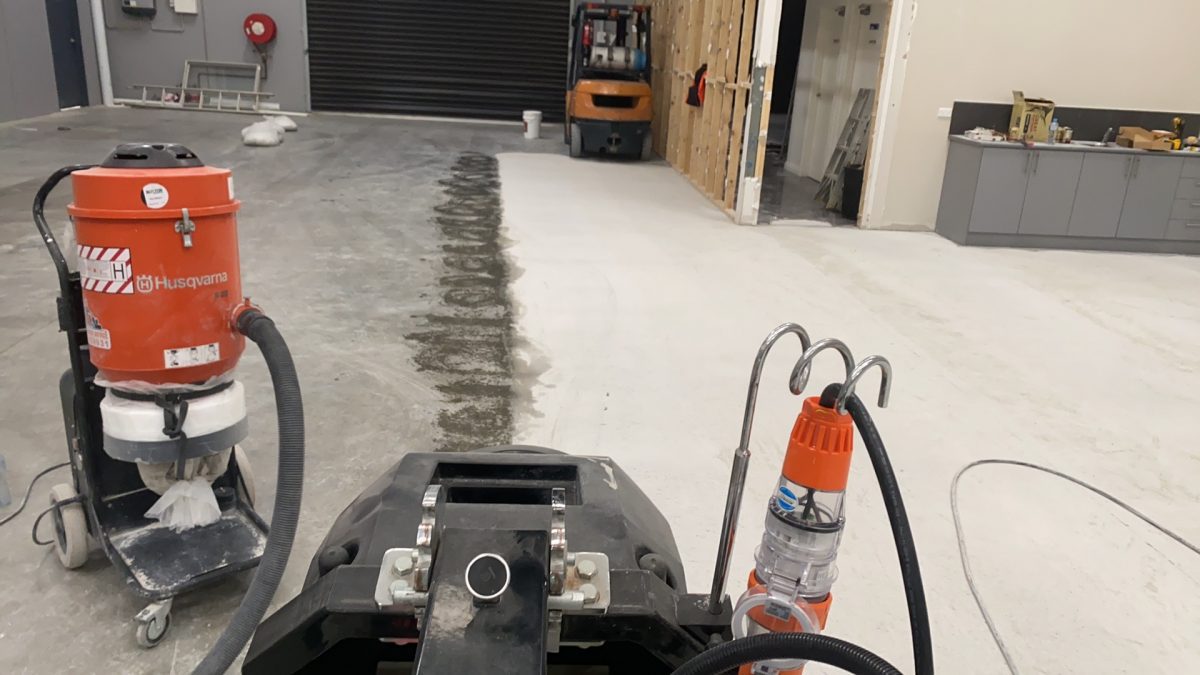
Concrete Repairs
Concrete floor repair is a demanding renovation job that not only needs expertise; it requires a spe....
Read More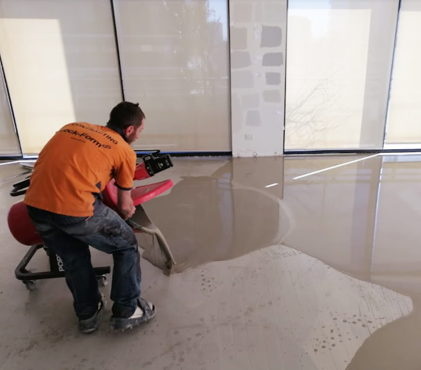
Floor Levelling
Basement floors or slab floors typically sink and become uneven over time due to many factors. But t....
Read More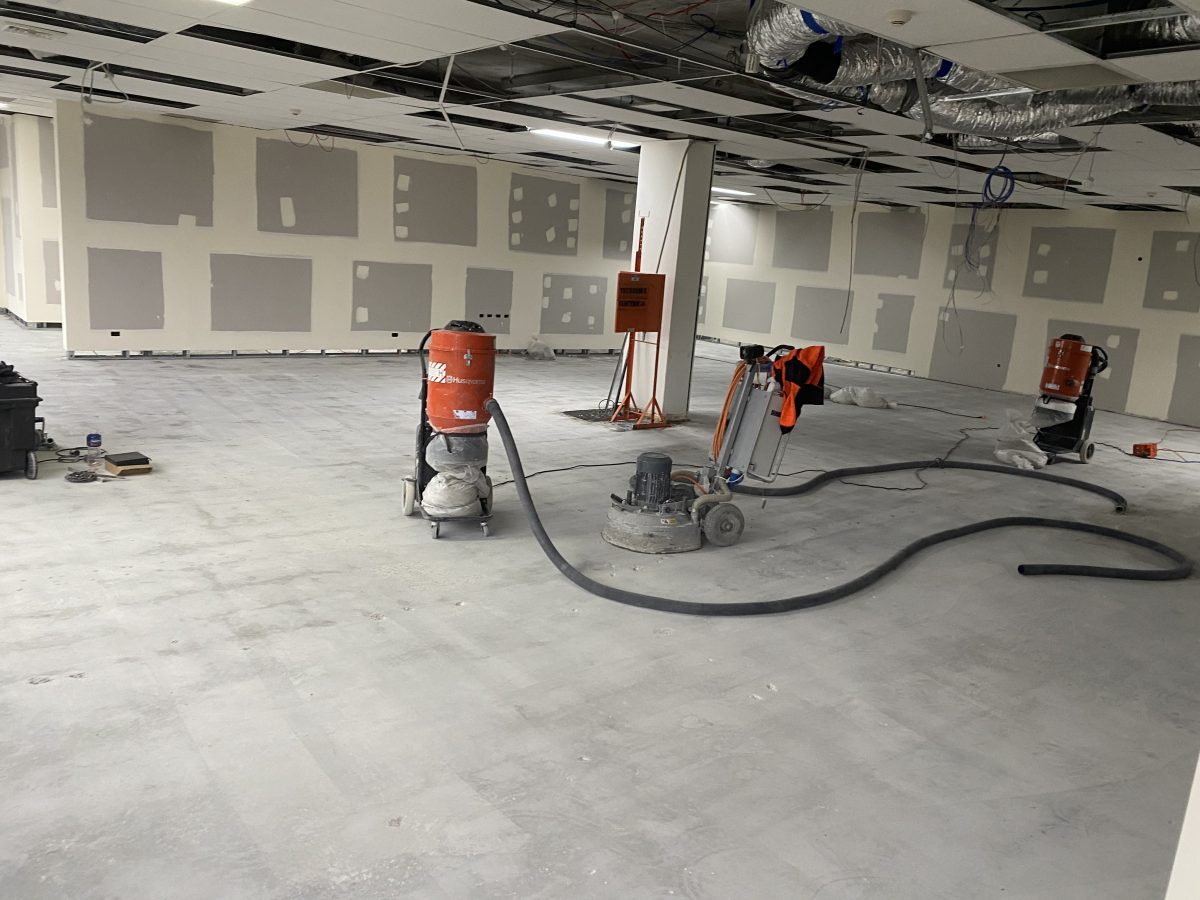
Floor Preparation
If you plan to overlay or restore existing concrete, proper surface preparation is essential to achi....
Read More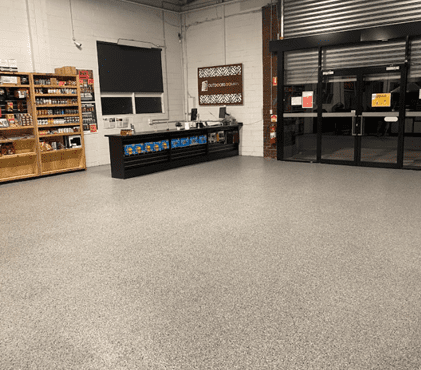
Epoxy Flooring
WHAT IS EPOXY FLOORING? & WHAT ARE THE DIFFERENT TYPES OF EPOXY FLOOR COATINGS? When it comes t....
Read More
Grind & Seal
What Are Grind and Sealed Concrete Floors? Grind and sealed concrete is exactly like its name. The ....
Read More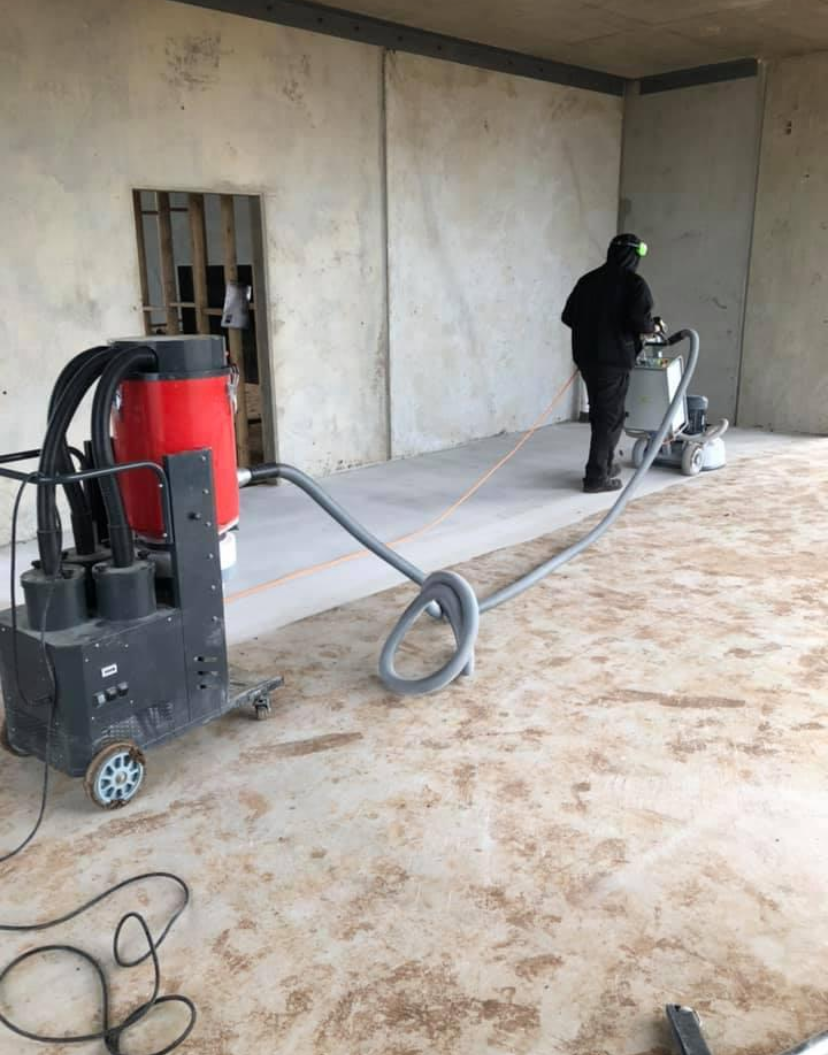
Concrete Grinding
WHAT IS CONCRETE GRINDING? Concrete grinding is the process of smoothing rough concrete surfaces. D....
Read More
Concrete Polishing
Polished concrete is the ultimate no-wax flooring material. With the proper floor grinding equipment....
Read More